Sandblasting
If the item you want to paint has rust, scale, old paintwork, then you will most likely need sandblasting. Sandblasting chambers are especially useful for workshops working with untouched raw materials, for example, steel sheets or pipe blanks with oxidation sites or welding residues. Since the material from the abrasive treatment gets into all places, it is necessary to remove all threaded or lubricated parts, such as bearings, bolts/nuts, clamps.
Sandblasting is well suited for objects with complex shapes, immersion is better for sheet metal panels, because sandblasting generates heat that can deform sheet metal.
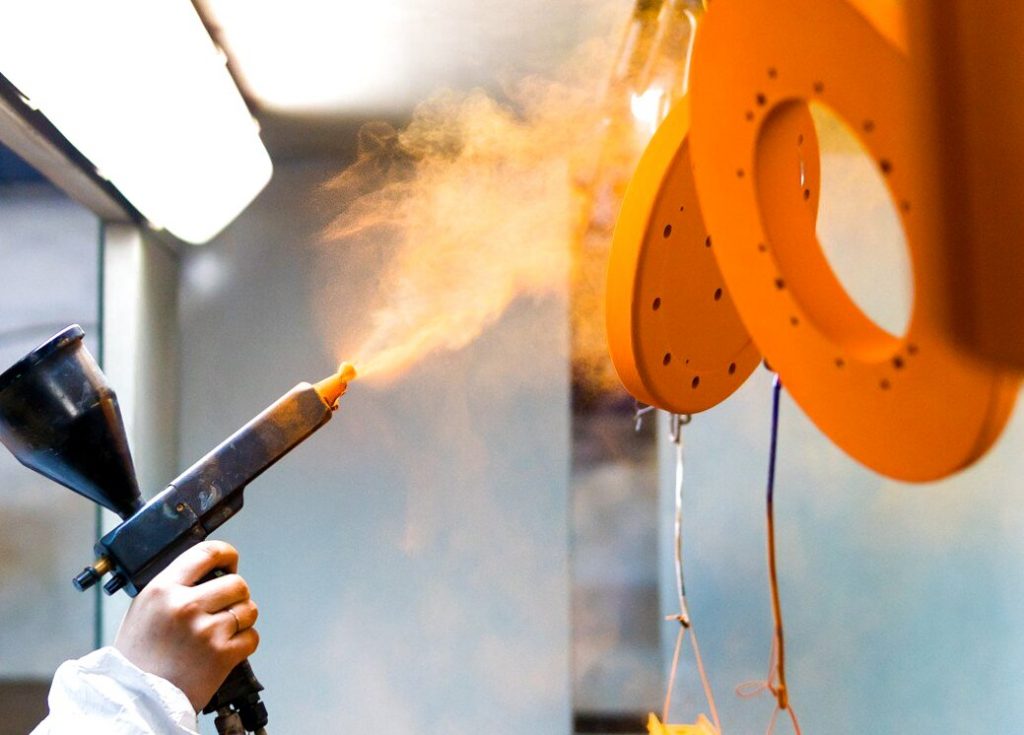
When the part is processed, the surface acquires a roughness that increases adhesion during painting.
Rinsing
After cleaning, the rinsing stage begins. It is important to remove any chemical residue. After rinsing, dry the surface as quickly as possible to avoid rust.
Phosphating and chromating
Phosphating improves adhesion during painting, improves anticorrosive properties. The process is carried out on a well-cleaned surface of steel, sometimes non-ferrous metals.
There are two types of phosphating: iron phosphating and zinc phosphating. Both of them are technically called conversion coatings, i.e. the action of solutions “converts” several microns of the metal surface either into iron phosphate or zinc phosphate. Phosphating, as a rule, is carried out in several stages, including degreasing, washing before and after the process, phosphating itself.
Iron Phosphate coating
When steel is treated with acid salts of orthophosphoric acid and monovalent metals, a layer of amorphous phosphate iron forms on the surface. This is the most convenient and inexpensive way to prepare for powder coating.
Zinc Phosphate coatings
Phosphating with zinc salts leads to the formation of coatings of a crystalline structure. Such phosphating is more expensive compared to the application of amorphous iron phosphate, but it allows you to get better coatings, it is considered the best surface preparation before powder coating.After phosphating the product, it is dried in a drying chamber.
Chromating the surface
Chromate treatment (chromating) is most often subjected to aluminum and its alloys. Treatment with compounds containing chromium increases the protective properties of the metal. Conversion coatings based on chromium phosphate and chromate have become the most widespread.
Due to the possible porosity of the conversion coatings, they are finally washed with passivating solutions containing compounds of six or trivalent chromium, their combinations with other components that have a passivating effect.
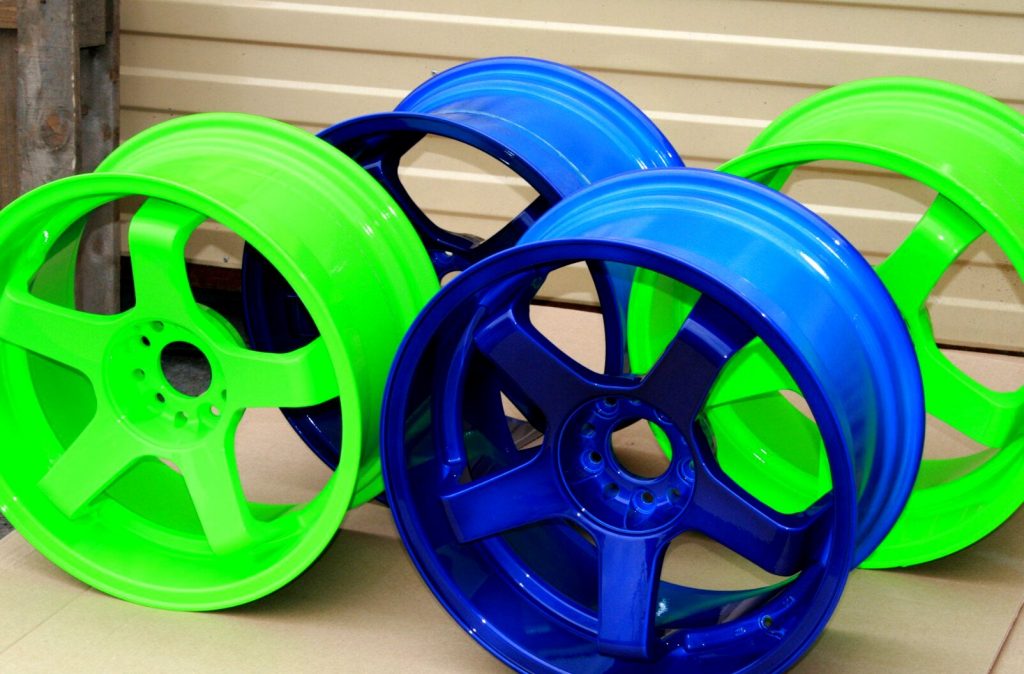
When preparing the surface, a large amount of water is used. The purity of the water and the degree of its contamination must be constantly monitored. Very important factors are the hardness of water, the presence of soluble and suspended substances in it.
Recently, alternative processes have been developed to avoid the use of chromates, since they are toxic. Titanium zirconium and silanes have similar anticorrosive and adhesive characteristics.